Виды технологий монтажа и пайки печатных плат
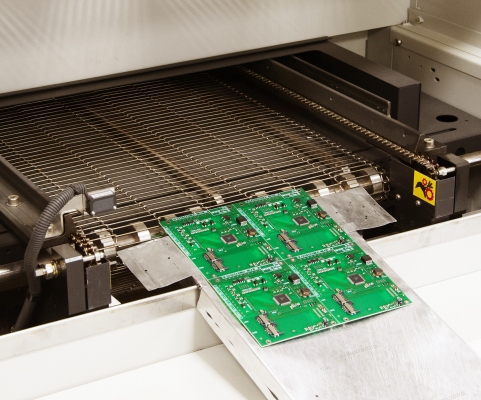
Пайка элементов на печатные платы, пластинки из диэлектрического материала с токопроводящими дорожками на поверхности, осуществляется следующих видов монтажа - вручную, на полуавтоматическом или автоматическом оборудовании.
Существует два способа создания электронных микросхем:
- TNT (DIP) – штыревые контакты элементов выводятся на наружную часть платы через отверстия;
- SMD – контакты электронных компонентов фиксируются на металлизированных дорожках на поверхности платы.
При создании сложных микросхем выполняют смешанный монтаж. На плату с металлизированными отверстиями и дорожками на первом этапе монтируют SMD-элементы, на втором – DIP-элементы.
Виды паек печатных плат
По количеству синхронно устанавливаемых элементов, пайка плат бывает:
- групповой (одновременной), с термическим воздействием на всю поверхность пластины из диэлектрика;
- индивидуальной (селективная пайка печатных плат), с воздействием на конкретный участок поверхности.
В зависимости от технологии, различают следующие виды пайки:
- волной припоя;
- в паровой фазе;
- ИК-нагревом;
- конвекционным методом;
- лазером.
Указанные технологии позволяют существенно ускорить монтаж за счет групповой пайки элементов на печатные платы на автоматизированном оборудовании.
Пайка волной припоя
Технология разработана в 50-х годах прошлого века и используется при серийном производстве электронных приборов.
На первом этапе на печатную плату устанавливаются электронные компоненты, после чего она попадает на конвейер. Там мест пайки покрывают флюсом, затем предварительно прогревают плату и перемещают над ванной с расплавленным припоем. Специальные сопла создают волну с гребнем специально рассчитанной высоты и формы, которая смачивает припоем контактные площадки и выводы установленных деталей.
В основном данная технология используется при DIP–монтаже, когда электронные компоненты размещаются с одной стороны платы, а контактные площадки и выводы – с другой. Пайка волной припоя может задействоваться и для крепления SMD-элементов. В этом случае компоненты требуется предварительно приклеить к плате специальным составом. Так как плата должна размещаться над ванной SMD-элементами вниз, расплавленный припой омывает не только плату, но и корпуса электронных компонентов. Так как не все элементы способны выдерживать высокий нагрев, это ограничивает применение технологии пайки волной припоя.
Конденсационная пайка (в паровой фазе)
Данная технология подходит для мелкосерийного производства печатных плат и позволяет осуществлять монтаж смд компонентов любого типа, не боясь перегрева.
Нагрев платы с электронными компонентами, предварительно установленными на паяльную пасту, осуществляется за счет конденсации пара в камере автоматизированной установки. Источник пара – химически инертная жидкость, не провоцирующая возникновения коррозии. Выбор жидкости с подходящей температурой кипения (от 160°С до 260°С) зависит от индивидуальных требований к условиям пайки и типа припоя (свинцовосодержащий или бессвинцовый).
Пар кипящей жидкости вытесняет воздух из камеры, поэтому пайка осуществляется в бескислородной среде. Так как температура пара стабильна, исключен перегрев компонентов и обеспечивается безупречная повторяемость процесса. Данный вид пайки печатных плат позволяет создавать изделия любой сложности, включая гибкие платы, многослойные, на алюминиевом основании.
Пайка инфракрасным излучением
Технология инфракрасной пайки заключается в воздействии сфокусированным потоком ИК-лучей на участки объекта пайки. Для изготовления плат используется полуавтоматическое и автоматическое оборудование. По типу источника излучения различаются три вида установок:
- ламповые;
- панельные;
- комбинированные, с лампами и панелями.
Конструкция усовершенствованных ИК-печей позволила избавить технологию от ряда недостатков – предусмотрен отвод испарений флюсов, обеспечивается максимально равномерный нагрев изделий, без появления горячих точек, за счет предварительного прогрева плат.
Инфракрасная пайка:
- подходит для серийного и массового изготовления печатных плат;
- не требует предварительно приклеивать компоненты при одностороннем монтаже;
- позволяет изготавливать платы с высокой плотностью расположения компонентов;
- дает возможность фиксировать электронные компоненты всех типов, включая элементы с контактными площадками, скрытыми под корпусом;
- позволяет осуществлять дифференцированный подвод тепла – обеспечивать разный режим нагрева для разных зон платы.
При этом важно учитывать, что для каждого типа печатного узла требуется правильно подобрать режим пайки. Кроме того, есть ряд ограничений, касающихся материала изготовления печатных плат, выбора элементной базы.
Конвекционный метод
Конвекционная пайка – широко распространенная технология, при которой нагрев паяльной пасты осуществляется за счет принудительной конвекции горячего воздуха. Чтобы минимизировать процесс окисления, пайка может производиться в инертной среде.
Процесс проходит в четыре этапа:
- предварительный нагрев платы с установленными компонентами;
- стабилизация (выравнивание температуры);
- оплавление;
- охлаждение.
Для конвекционной пайки используются специальные камеры с регулировкой температуры либо конвейерные печи, где плата перемещается из одной температурной зоны в другую.
Температурный профиль пайки элементов на печатные платы формируется с учетом вида оборудования, состава паяльной пасты, материала изготовления печатной платы, характеристик электронных компонентов.
Лазерная технология
Лазерное излучение – мощный источник тепловой энергии, воздействующий локально. При пайке электронных компонентов нагреву подвергается отдельный вывод или ряд выводов. При этом современные установки для сборки электронных модулей позволяют осуществлять монтаж со скоростью около 10 выводов в секунду, что приближает производительность такой селективной пайки к классическим видам групповой.
Пайка лазером незаменима при создании сложных микроэлектронных устройств. К достоинствам технологии относят:
- минимальное температурное воздействие на корпус электронных компонентов, что позволяет припаивать термочувствительные элементы без риска перегрева;
- низкую степень окисления припоя;
- возможность изготовления модулей с высокой плотностью монтажа и минимальным шагом выводов без возникновения шариков припоя и перемычек.
Весь технологический цикл может быть автоматизирован и включать в себя лазерный контроль качества паяных соединений.
От других видов паек печатных плат лазерная отличается более высокой стоимостью оборудования.